Introduction to Audio System
Audio System is a system of electronic equipment for recording or reproducing sound.
The first influence upon the car audio system was the radio. Invented in the early 1900's (around the same time cars became popular) it however didn't gain commercial status until the 1920's when the first commercial boomed occurred. In 1922, a historic date for the car audio system, George Frost was the first person known to experiment with car radio with his own Ford car. Then in 1925, the first official listing of a car radio occurred, which was followed in 1927 with the first mass produced car radio, the Transitone TH-1.
1930: First Commercial In-Car Radio
The history of car audio dates back to the 1930s, when the Galvin brothers introduced the first car radio, named Motorola ('motor' meaning motion and 'ola' meaning sound). Innovations kept happening in many parts of the world. It took another forty years to develop audio amplifiers, in a quest to develop something just more than a radio. Since then, there have been more and more sophisticated devices which can stand the temperatures and vibration of automobiles. Modern speakers are not even visible, but produce good acoustics and sound quality.
AM was the undisputed king of the airwaves in 1952, but that didn’t stop Blaupunkt from introducing the first in-car FM radio.
1953: Becker Mexico Introduced
Becker’s iconic Mexico radio launched this year, arguably the first
premium in-car radio. It had AM/FM and the first fully automatic
station-search button.
1955: First “Music On Demand”
Starting in 1955, Chrysler offered a small turntable in its high-end
cars, playing proprietary seven-inch records with about 45 minutes of
music. It was a bust.
1963: First All-Transistor Radio
A number of manufacturers introduced transistors to their aftermarket
car radios in the early 1960s, but Becker’s Monte Carlo was the first to
be fully “solid state”—no vacuum tubes.
1965: First Eight-Track Tape Player
Predecessor to the cassette, the eight-track was a loser from the start
and was dead by the early ’80s. Ford and Motorola jointly introduced
in-car eight-track players this year.
1969: First Stereo
Becker’s Europa was the first in-car stereo setup, with the tuner amplifying two channels instead of one.
1970–1977: Cassette-Tape Players
The rollout of cassettes allowed for one of mankind’s greatest
achievements: the mix tape. This development also heralded the creation
of branded aftermarket cassette-tape players from Alpine and Pioneer,
among others.
1982: Bose Becomes First Premium Stereo System
Bose and GM’s Delco teamed up to offer the first “designer” stereo
system. Bose sank money into car-specific development; rather than just
producing an expensive head unit, it was marketing the entire system to
Oldsmobile, Buick, and Cadillac shoppers.
1985: First Factory-Installed In-Dash CD Player
While Sony had introduced an in-dash player the previous year, Becker’s
Mexico Compact Disc was the first to be factory installed (in Benzes, of
course).
Component Identification
The Head Unit

The head unit refers to the main device that serves as the source of the sound or simply the radio that is installed in the car's dashboard. The unit has a radio receiver and tuner component that receives radio frequencies through an antenna. The tuner is used to select or adjust radio frequencies or broadcast bands. The unit has other components, such as a disc player that plays different types of disc formats, a preamplifier that sends sound signals to the speakers and an equalizer that shapes the sound. The radio unit has an interface for control over the unit's different functions such as the volume and menu functions. The head unit is powered by the car's electrical distribution system. Wires and cables also connect the head unit to all the other components in the audio system.
Read more: How Does a Car Audio System Work? | eHow.com http://www.ehow.com/how-does_4928715_car-audio-system-work.html#ixzz2Q2XhnK8t
The head unit refers to the main device that serves as the source of the sound or simply the radio that is installed in the car's dashboard. The unit has a radio receiver and tuner component that receives radio frequencies through an antenna. The tuner is used to select or adjust radio frequencies or broadcast bands. The unit has other components, such as a disc player that plays different types of disc formats, a preamplifier that sends sound signals to the speakers and an equalizer that shapes the sound. The radio unit has an interface for control over the unit's different functions such as the volume and menu functions. The head unit is powered by the car's electrical distribution system. Wires and cables also connect the head unit to all the other components in the audio system.
Read more: How Does a Car Audio System Work? | eHow.com http://www.ehow.com/how-does_4928715_car-audio-system-work.html#ixzz2Q2XhnK8t
The Amplifier

A car stereo system has to have an amplifier to increase the power of an audio signal so it's strong enough to move the speakers and create sound. Amplification is a two-stage process handled by a preamp and a power amplifier.
A car stereo system has to have an amplifier to increase the power of an audio signal so it's strong enough to move the speakers and create sound. Amplification is a two-stage process handled by a preamp and a power amplifier.
The preamp is usually housed inside the head unit and takes data from a radio, CD player or other audio source and prepares it for the power amplifier. This process includes slightly boosting the audio signal, which makes it compatible with the input of the power amplifier and ensures that it's resistant to noise that can radiate from other electronics in a vehicle. The power amplifier then takes the preamp's low-level signal and significantly boosts it so it can move the speakers and create sound.
Many head units have a small, built-in low-power amplifier that can "drive" smaller speakers. This allows the audio system to be reduced to just a head unit and a few speakers. But better sound requires more power. So higher-end systems have separate power amplifiers that are mounted away from the head unit due to their size and the heat they generate. We cover the details of "outboard" amplifiers in a separate article in this series.
The Speakers
A speaker is important to the final output of an original car audio system. Just like the singer’s voice, a sweet voice will produce fantastic sound output. The role of the speakers is to convert audio electrical signal to a sound signal and let the signal radiates in the surrounding medium. The volume can be adjusted by using either an appropriate knob or buttons on the head unit. Changes can also be made to the amount of base and treble being supplied by the speakers. The head unit makes these changes by adjusting the pitch and frequency output for the speakers. The most common design for car speakers is the tapered design. This is because of the space limitation inside the vehicle for car stereo installation. The tapered design makes it possible to expand the effective area of the diaphragm, and this effective area determines the low frequency response of the speaker. In other words, the tapered design can enhance the bass effect if a car radio system without the installation of bass case..
Crossovers
A crossover is used to distribute the audio between the various speakers in your car audio system. They are available in two varieties which are active and passive.
![]() |
Active crossovers are placed between your car stereo output and the amplifiers feeding your speakers. They offer many advantages over their passive counterparts. Most crossovers offer the ability to alter the frequency ranges and levels dedicated to each amplifier. The main disadvantage is that they are more expensive than their passive counterparts.
|
Passive Crossover
![]() |
Passive crossovers consist of capacitors and inductors. A capacitor's impedance reduces as the frequency increases whereas an inductor's impedance increases with frequency. These characteristics can be used to filter the frequencies fed to each speaker in the system. The choice of these components is very simple and can be found using some simple equations.
|
The advantages of a passive crossover is that they are very cheap, easy to build and can be tailored exactly to your requirements.
The disadvantages are that they have to be placed between the amplifier and the speaker. This introduces a loss in the system which means less power to the speakers! Another disadvantage is that the crossover is tailored to a set of speakers. If these speakers are changed the crossover may require redesigning.
Equalisers
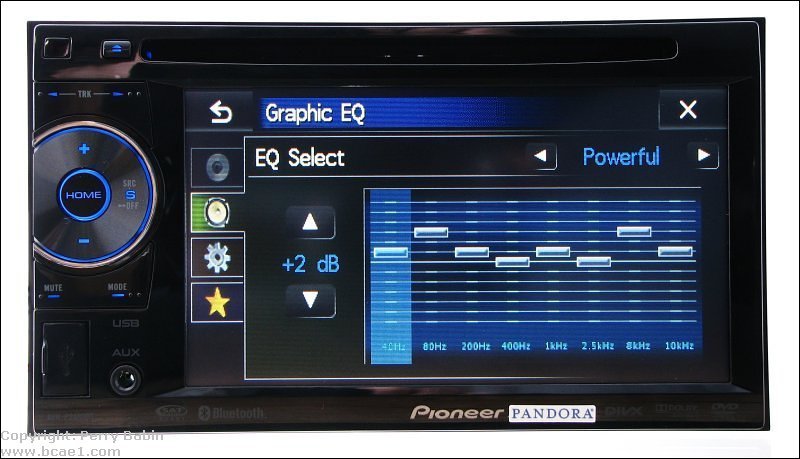
An equaliser enables the frequency response of the system to be 'tweaked'. It allows adjustment of various frequencies across the audio spectrum for example 20, 40, 80, 160, 315, 630 Hz and so on.
The purpose of an equaliser is not to fix problems with the system such as too much mid range or too much bass. If this is the case these issues should be addressed by reducing and increasing the appropriate amplifier gains. An equaliser should be used to flatten the audio response of the entire system. This means that if it is used correctly the gain/cut controls should remain very close to the centre.
Basic Operation
This diagram shows the head unit's RCA output jacks driving the RCA inputs of the amplifier. The signal is a full range signal which, as you can see, is reflected in the frequency response graph. It shows that all of the frequencies across the audio spectrum are being reproduced at the same level. The relative signal levels of the head unit's output and the amplifier's output are shown by the sine waves in the upper right hand corner of the diagram. You can see that the output from the amplifier is larger in magnitude (because the amplifier amplifies the head unit's output signal). In a real system, the difference in magnitude between the two waveforms would actually be much larger than shown but you get the picture (or the diagram :-).
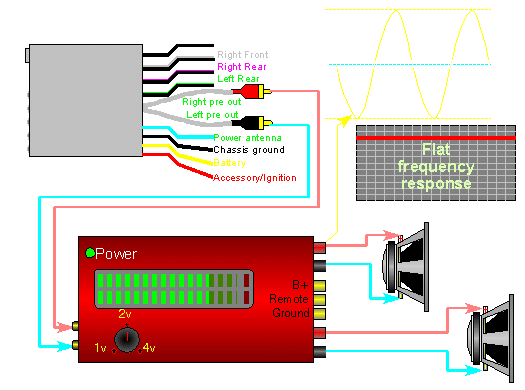
Benefits Of Audio System
In this day and age, practically everybody can drive. The need to travel around for work as well as for leisure purposes has meant that driving has become almost an essential skill needed for everyday life. The fact that we do use our cars so often means that we can sometimes get a little bored of driving. That is when a slight distraction is needed to keep us focused and to make driving that little bit more pleasurable. This distraction generally comes in the form of a car audio system. A car audio system allows you to listen to your favorite music whilst you are driving.
Basic Operation
This diagram shows the head unit's RCA output jacks driving the RCA inputs of the amplifier. The signal is a full range signal which, as you can see, is reflected in the frequency response graph. It shows that all of the frequencies across the audio spectrum are being reproduced at the same level. The relative signal levels of the head unit's output and the amplifier's output are shown by the sine waves in the upper right hand corner of the diagram. You can see that the output from the amplifier is larger in magnitude (because the amplifier amplifies the head unit's output signal). In a real system, the difference in magnitude between the two waveforms would actually be much larger than shown but you get the picture (or the diagram :-).
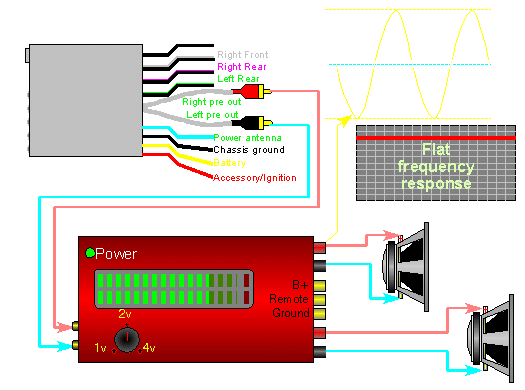
Benefits Of Audio System
In this day and age, practically everybody can drive. The need to travel around for work as well as for leisure purposes has meant that driving has become almost an essential skill needed for everyday life. The fact that we do use our cars so often means that we can sometimes get a little bored of driving. That is when a slight distraction is needed to keep us focused and to make driving that little bit more pleasurable. This distraction generally comes in the form of a car audio system. A car audio system allows you to listen to your favorite music whilst you are driving.